By Eleftherios Tsivolas, Ph.D., Multi-Physics Modeling and Simulation Technical Lead
Speed and precision in food product development are more critical than ever in today’s competitive market. Whether you’re creating better-for-you protein snacks, optimizing extrusion parameters, or scaling up new processes, innovation must be fast, cost-effective, and grounded in solid science. However, striking this balance remains a major challenge, particularly when dealing with the complex thermal and fluid dynamics of food processing, and the ever-present risk of developing a product that ultimately fails with consumers due to poor taste, texture, mouthfeel, or other key sensory attributes.
This is where Computational Fluid Dynamics (CFD) modeling becomes a game-changing solution. Borrowed from industries like aerospace and energy, CFD provides deep, physics-based insight into how materials flow, mix, and heat during processing. For CPG brands, it enables accurate simulation of extrusion, drying, and mixing operations, helping teams identify and address potential issues early, before investing in costly and time-consuming physical trials.
Why CFD Is Essential for High-Performance Product Development
CFD-based modeling solves critical challenges in modern processing and manufacturing by delivering deep, physics-based insight into how fluids and energy behave in complex systems. In industries where performance, precision, and quality are non-negotiable, such as food processing, energy, and advanced manufacturing, understanding and predicting these behaviors is essential to avoid costly errors, delays, and product failures.
By numerically solving the governing equations of mass, momentum, and energy conservation, CFD enables engineers to simulate the real-world physics of fluid flow, heat transfer, phase changes, and chemical reactions with high accuracy. These simulations go beyond theoretical assumptions, offering data-driven representations of how systems behave under actual operating conditions before physical testing begins.
This matters because many critical product and process failures, especially in the food industry, stem from poorly understood interactions between flow, temperature, shear, and material properties. Problems like inconsistent texture, off-flavors, poor mouthfeel, or structural breakdowns can originate at the microscopic level but have direct and costly implications at the consumer level. CFD helps identify and address these issues early in development, reducing the risk of launching a product that performs well in theory but fails in practice.
For example, in thermal-fluid systems, CFD can simulate how materials behave across a range of temperatures, pressures, and flow regimes. This includes predicting how shear affects dough elasticity, how heat is distributed in extrusion barrels, or how drying rates influence final texture. Such insights are vital for achieving consistency, food safety, and consumer satisfaction without relying entirely on expensive and time-consuming physical prototyping.
The strategic benefits of CFD are hard to ignore:
- De-risk product development by revealing processing and formulation issues early, avoiding consumer-facing failures.
- Virtual experimentation enables rapid testing of multiple design and process variables without the cost or time of physical trials.
- Accelerated innovation cycles by enabling faster iterations and more informed decision-making in a simulated environment.
- Reduced R&D costs through less material waste, fewer failed batches, and minimized trial-and-error.
- Optimized process and equipment design that translates into higher efficiency, lower energy use, and better product quality at scale.
In short, CFD is not just a modeling tool. It is a strategic enabler of innovation, quality assurance, and risk mitigation in complex processing environments. For food & snack companies operating in competitive, quality-driven markets, adopting CFD means making smarter, faster, and more reliable decisions from formulation through full-scale production.
From Simulation to Smart Innovation: PIPA’s Integrated Approach
At PIPA, we go beyond traditional CFD with our product development platform, Digital Extruder, a powerful system that integrates Computational Fluid Dynamics (CFD), generative AI (GenAI), and machine learning (ML) to accelerate food innovation and reduce the risk of market failure.
In food product development, high-fidelity simulations are essential for predicting how materials behave under complex processing conditions. However, achieving this level of accuracy often requires extensive computational resources, which becomes a bottleneck when thousands of simulations are needed for optimization. Digital Extruder addresses this challenge by balancing accuracy, fidelity, and computational efficiency, enabling rapid, precise simulations of fluid flow, heat transfer, and material behavior under real processing constraints.
What differentiates our approach is the integration of GenAI and ML. These technologies ingest and analyze large volumes of experimental and simulation data, learning from both past outcomes and evolving formulation requirements. By identifying the key process variables that most strongly influence product quality, such as texture, mouthfeel, or structural integrity, our models focus computational effort where it matters most. This targeted simulation strategy drives faster convergence, smarter exploration of the design space, and ultimately, better-performing products.
At the core of Digital Extruder is an intelligent, adaptive engine that continuously improves its predictive power. Instead of relying on static models, the platform refines its insights over time, integrating feedback from both digital and physical trials. This creates a closed-loop system where simulation, learning, and real-world validation inform one another, delivering a faster, more reliable pathway from concept to shelf-ready product.
Digital Extruder Platform: Connecting Formulation, Process, and Sensory Experience
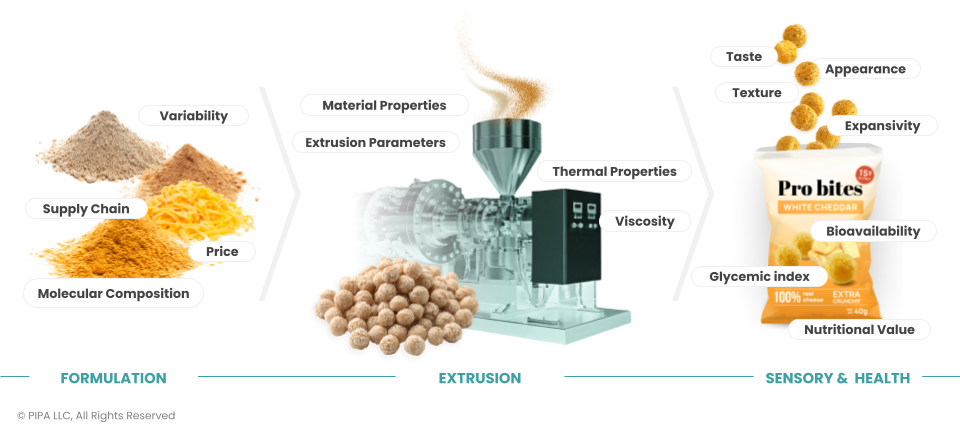
The Digital Extruder Platform is built to bridge the gap between technical process optimization and consumer product success. By combining physics-based simulation with AI-driven sensory modeling, it helps teams design not just efficient extrusion processes, but finished products that deliver on taste, texture, and nutrition.
Each component of the platform plays a distinct role in accelerating innovation while maintaining scientific depth and practical usability:
- Digital Extrusion Twin
A high-fidelity Computational Fluid Dynamics (CFD) model of twin-screw extrusion that simulates fluid flow, heat transfer, and material transformations. Supports multi-objective optimization of process parameters and material behavior. - Sensory Optimization
Uses machine learning models trained on real sensory and formulation data to predict and improve consumer-relevant attributes like texture, mouthfeel, and overall acceptability. Integrates process conditions and nutritional profiles to align technical output with sensory targets. - Conversational AI
A natural-language interface that allows users to query the system, receive instant, evidence-backed answers, and get recommendations on formulation changes, process tuning, and product positioning—without needing to be a simulation expert.
Together, these components form a unified platform that enables R&D teams to iterate faster, reduce trial-and-error, and develop products that are technically sound, nutritionally balanced, and sensorially appealing.
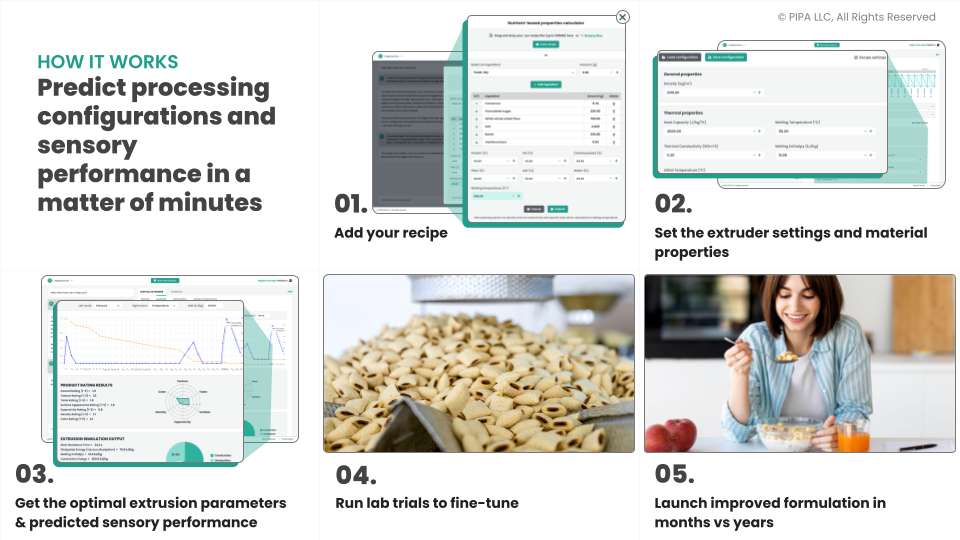
Read how snack company Rivalz used the Digital Extruder Platform to accelerate product development, launching its core snack line nearly 4x faster and at roughly 3x lower cost than typical industry benchmarks, going to market in under one year for $1.2 million instead of the usual 3–5 years and $4 million.
Extrusion & Food Formulation Digital Twins: Turning Science into Scalable Advantages
As food extrusion systems grow more complex, driven by rising demand for high-protein formats, clean-label reformulations, and energy-efficient processing, traditional trial-and-error development approaches fall short. Speed, accuracy, and adaptability are now essential for staying ahead in an increasingly competitive market.
PIPA meets this challenge by merging high-fidelity CFD simulation with the speed and intelligence of AI and machine learning. This powerful combination transforms product development from a time-consuming, manual process into a data-driven, automated cycle of continuous improvement.
With PIPA’s Digital Extruder platform, development timelines shrink from weeks to days. Teams gain the ability to test, iterate, and optimize with precision, reducing physical trials, cutting costs, and improving confidence in the final product. Whether you’re a food scientist refining formulations, a process engineer scaling production, or an executive making strategic investment decisions, the impact is the same: faster innovation, reduced risk, and a measurable edge in product performance and market success.
Simulation-led, AI-enhanced innovation isn’t just an emerging trend. It’s a fundamental shift in how modern food products are conceived, validated, and delivered. To learn more about our product development platform, get in touch with our team.